The blower is driven by soft starter instead of direct starter. When the blower reaches rated speed, it switches to normal 380V power supply loop. A Mitsubishi FX2-48MR PLC and a AB 150-B360NB1 soft starter are used to control the starting upstate blowers of four blowers.
Main circuit wiring is shown in (the main circuit of blowers 2~4 is omitted). ST is the soft starter, K11, K21, K31 and K41 are the soft starter contactor of blower ~4 respectively, K1 is the contactor of normal power supply circuit of blower 1, and the main circuit of blowers 2~4 and blower 1 are connected to the same distribution bus. When the blower needs to be started, PLC sends signals to make the soft starter work, and the corresponding contactor in K1K4 is connected. The blower is driven by the soft starter. When the speed reaches normal, PLC sends signals to make the main contactor in the normal power supply circuit Kll~K41 connected, and the blower switches to the normal 380V circuit for power supply, and the soft starter quits operation.
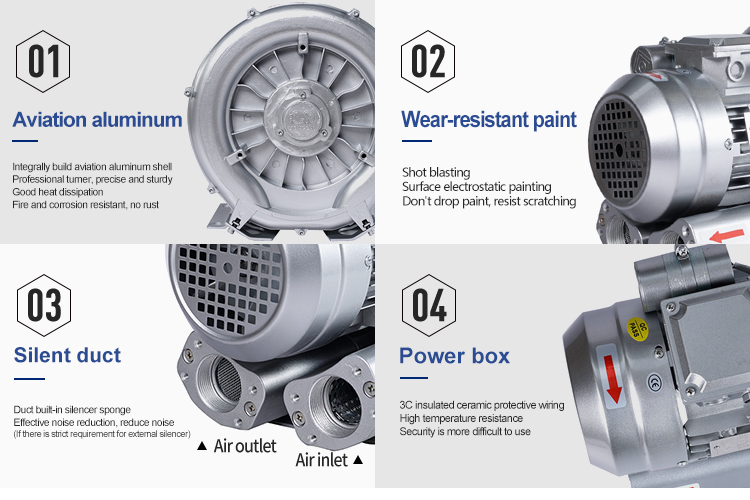
Special attention should be paid to that the three-phase phase sequence of the normal power supply loop and the soft start loop cannot be connected wrong when wiring, otherwise it will cause the accident of direct short circuit between the phases.
PLC input and output point allocation in the control system PLC input and output point allocation as shown. In the input points, 1, 12, 3 and 14 are the request starting signals of 4 blowers respectively, K1, K2, K3 and K4 are the main contactor status signals of 4 blowers, Kll, K21, K31 and K41 are the output contactor status signals of soft starters, and KST is the full conduction communication signal of soft starters.
Among the output points, K11, K21, K31 and K41 are soft start output contactors, and KYI, KY2, KY3 and KY4 are switching relays.
Typhoons first second third typhoon fourth typhoon comes tractor tractor tractor tractor to 3 process design for the blower control system for four blower design, the main program using query mode control can meet the real-time requirements, the main program, as shown in the process, such as shown in 1 machine processes such as wind, wind machine 1 program ladder diagram as shown below. After the transformation of the blower operation, there has been no fault, so that the stability of the control system has been greatly improved, to ensure the safe and normal operation of the factory production device.
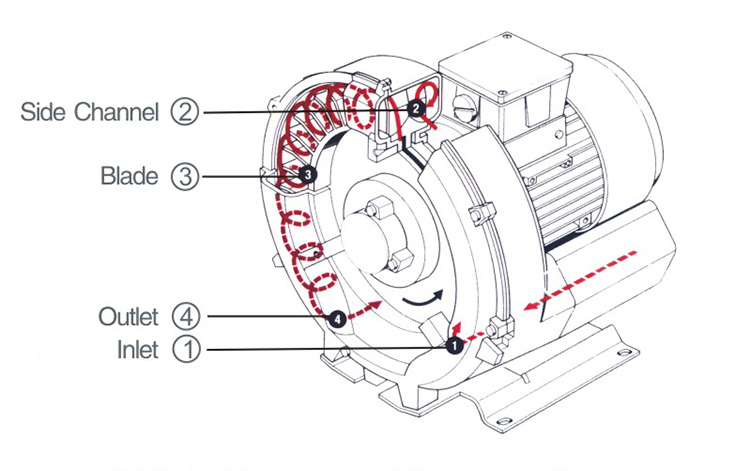
The main program flow, the wind machine program flowcharts into 1 typhoon machine any blower Is starting the first blower or a running jump to an end through soft starter contactor delay 0.8 s contact no and buy a fault to jump to the end of the time delay of 45 s thyristor no conduction jump to end all through the primary loop contactor delay Is contactor Is no and fault Switch to end system reset and return to subroutine return to No. 1 wind machine subroutine ladder diagram (edit leaf sail) Programmable controller motor selection application should choose temperature regulating electric iron, its heating up fast, after reaching the set temperature will be constant temperature. When blower irons clothes, he can first iron the ones with lower temperature resistance after power on, then iron the ones with higher temperature resistance after the temperature rises, and then iron some of the ones with lower temperature resistance after power off