In the world of industrial equipment, reliability and durability are paramount. When it comes to side channel blowers, these qualities become even more crucial, especially when the environment is hazardous. This article explores the art of designing side channel blowers for challenging environments, ensuring optimal performance even in adverse conditions.
Challenge of Hazardous Environments
Understanding the Hazards
Before delving into the design aspects, it's essential to grasp the unique challenges posed by hazardous environments. These environments often contain elements such as:
Explosive Gases: The presence of flammable gases demands equipment with intrinsically safe designs to prevent ignition.
Chemical Exposure: Corrosive chemicals can deteriorate equipment rapidly, necessitating materials and coatings that can withstand such exposure.
Dust and Debris: In environments with high levels of dust and debris, a blower's intake must be designed to prevent clogging and damage.
Designing for Durability
Material Selection
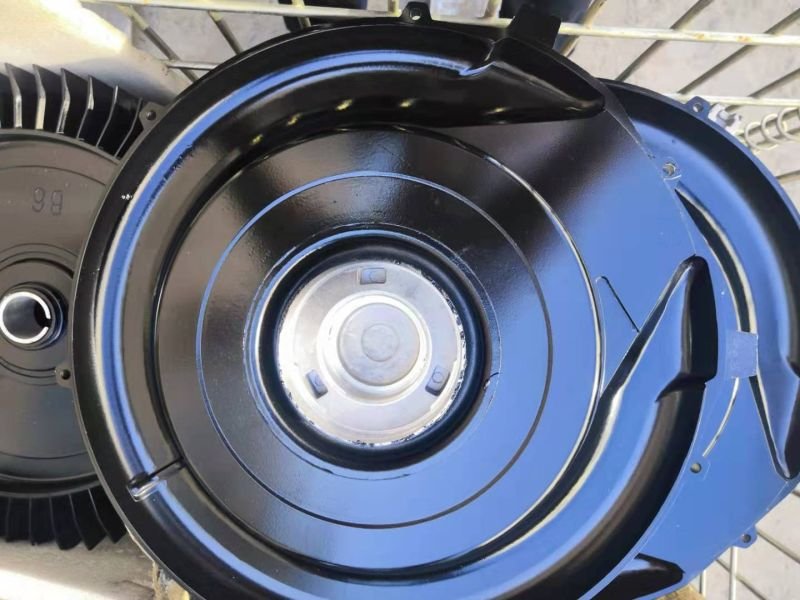
Selecting the right materials is the first step in crafting side channel blowers for hazardous environments. Stainless steel and corrosion-resistant alloys are commonly used to ensure longevity and resistance to chemical corrosion.
Intrinsically Safe Motors
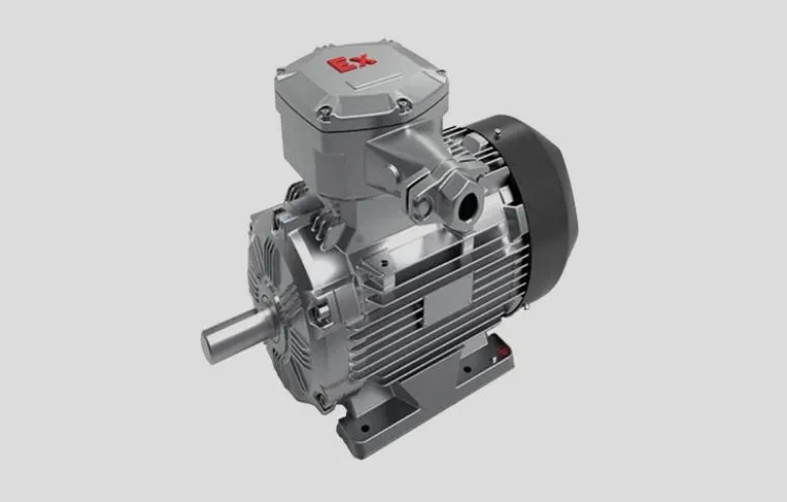
In potentially explosive atmospheres, the blower's motor must be intrinsically safe. This means it won't produce sparks or heat that could ignite flammable gases. Additionally, motors should be sealed to prevent dust and debris ingress.
Precision Engineering
Tight Tolerances
To maintain optimal performance, side channel blowers for hazardous environments are engineered with exceptionally tight tolerances. This precision minimizes air leakage and ensures efficient operation.
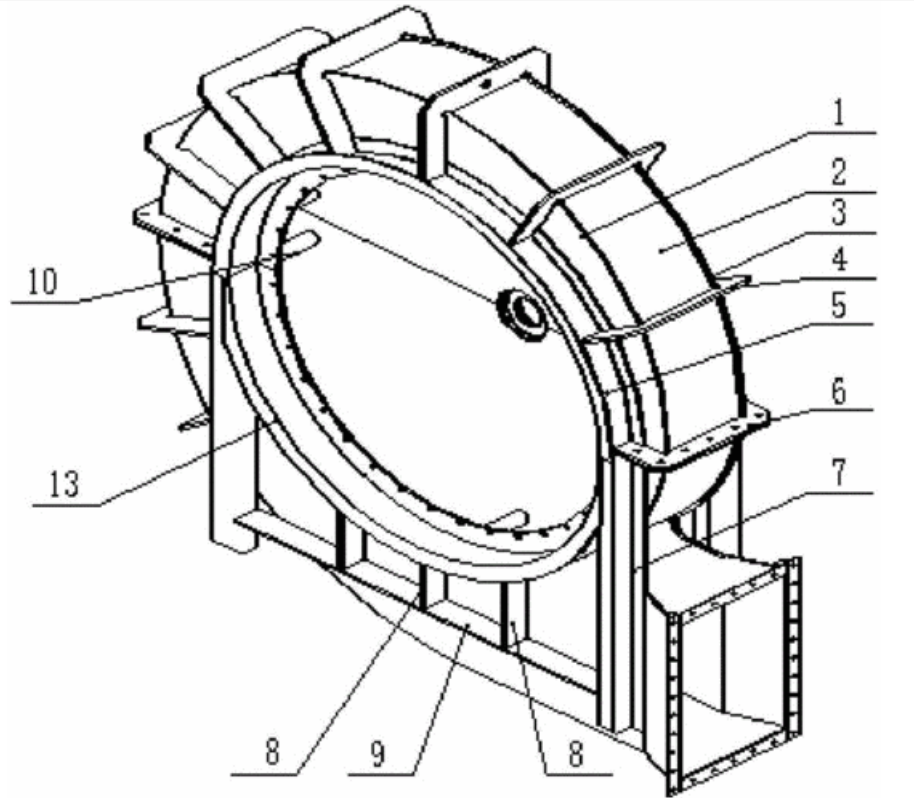
Balanced Impellers
Balanced impellers are critical to reducing vibration and noise while maximizing the blower's lifespan. Precision balancing techniques are employed to achieve this.
Protective Measures
Sealed Bearings
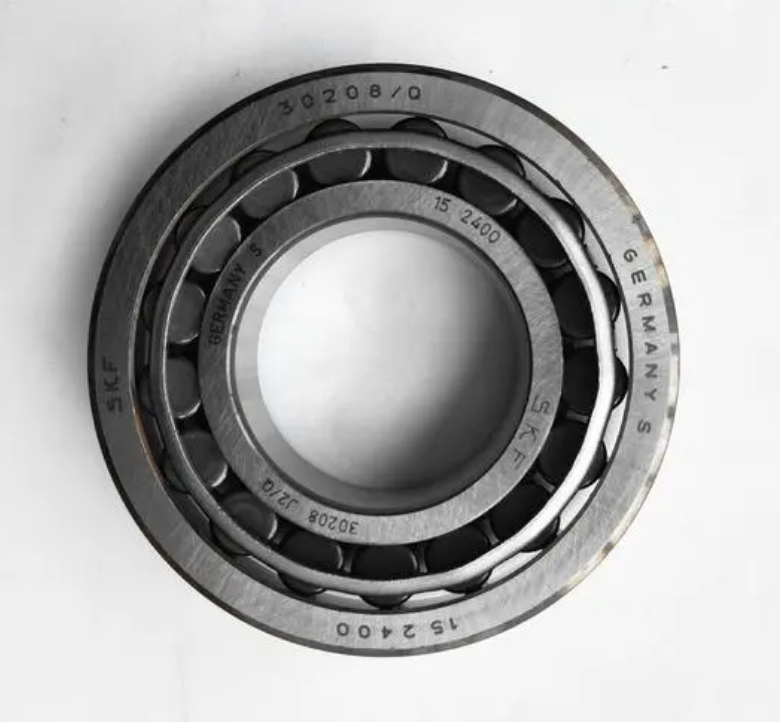
Sealed bearings are used to protect the blower's internal components from dust, moisture, and contaminants. This extends the blower's operational life.
Ingress Protection (IP) Ratings
Blowers are often designed with high IP ratings to safeguard against the intrusion of solids and liquids. IP65 and above are common ratings for hazardous environments.
Rigorous Testing
Quality Assurance
Before entering the market, side channel blowers designed for hazardous environments undergo rigorous testing. This includes performance assessments, endurance tests, and compliance checks with safety standards.
Field Testing
In some cases, field testing is essential to validate a blower's performance in real-world conditions. This ensures that it meets the demands of the specific environment it will be deployed in.
Conclusion
In hazardous environments, the design and manufacturing of side channel blowers are a blend of science and craftsmanship. Precision engineering, material selection, and stringent testing are all part of the process to create equipment that can withstand the harshest conditions.
As industries continue to push the boundaries of where they operate, the demand for reliable and durable side channel blowers will only increase. These specialized blowers are the unsung heroes that keep operations running smoothly in environments where others fear to tread.